In the dynamic world of manufacturing, efficiency, accuracy, and continuous improvement are not just goals but necessities for staying competitive. The adoption of digital tools, particularly work instruction software has become a pivotal aspect of modern operational productivity strategies.
Tech-enabled services like guided work instruction software are vital to the movement to make business operations more productive, cost-effective, and efficient. Paperless work instructions can also overhaul your team’s learning experience, making it more engaging and informative so that they can upgrade their skills and do their jobs correctly the first time, every time.
This guide is designed to walk you through the basics of work instruction software, focusing on its role in manufacturing for improving training and operational enablement. We’ll also explore the top 10 options available to help you make an informed decision.
Understanding Guided Work Instruction Software
Guided work instruction software—also called visual work instructions software and digital work instructions software—provides a digital platform for creating, distributing, managing, and tracking step-by-step instructions for tasks or processes. In manufacturing, this translates to detailed guides for assembly, maintenance, quality checks, and more. Guided instructions go a step further than typical work instructions, offering expert insights and walking learners through processes to achieve more successful outcomes. The shift from traditional paper manuals to digital instructions offers a multitude of benefits, including enhanced clarity, accessibility, and the ability to make updates to instructions in real-time.
Key Benefits:
- Improved Clarity and Comprehension: Multimedia features like videos, images, and 3D models help in understanding complex tasks.
- Enhanced Efficiency: Digital instructions can be easily accessed and followed, reducing training time and speeding up task completion.
- Reduced Errors: Accurate, easy-to-follow instructions minimize mistakes and improve overall quality by providing guidance a more dynamic way. Users are not forced to synthesize written text and abstract verbiage.
- Real-Time Updates: Immediate distribution of instruction updates ensures all team members have the latest information, so instructions are never obsolete.
- Performance Tracking: Built-in analytics allow for monitoring how instructions are used, identifying areas for improvement, and even developing new products or features.
The Evolution of Work Instructions
Work instructions are hardly a new invention, but how organizations create and share them has significantly transformed. Previously, companies provided their employees with basic printed manuals that they had to read and interpret. These guides might consist purely of text or include diagrams and images. In either case, they often included complex language and abstract descriptions that made tasks more difficult than they should be. Damaged, incomplete, or outdated instructions also posed a challenge, as a single lost page could halt a worker’s progress or cause them to complete a task incorrectly.
Eventually, organizations began scanning these hard-copy documents and putting them on computers or websites. These paper and PDF work instructions, which are still widely used today, are sometimes accompanied by videos that employees can watch during training sessions or independently on company computers.
Over the past several years, the integration of technology and work instruction processes has accelerated. Many of today’s manuals and guides go far beyond scanned pages and videos, featuring advanced capabilities, such as 360-degree views, interactive touch-screen manipulation, and immersive experiences.
The Importance of Guided Work Instruction Software
Guided work instruction software is a digital platform that allows companies or their solution partners to implement, manage, and share work instructions with employees. It allows you to be extremely specific in your instructions and outline step-by-step procedures to increase the quality of work and operational efficiency.
The level of detail in these kinds of instructions addresses a wide range of pressing issues, including:
- Training length: According to the 2024 research report, Technical Training Trends, Challenges, and Insights to Help You Get Ahead, half of senior executives are concerned about the length of their current training cycles. Guided work instruction software substantially shortens and improves training and learning time because it allows learners to engage directly with the material and gain a deeper understanding of processes and tasks.
- Errors and rework: In-depth work instructions make mistakes less likely because workers can focus on specific areas of importance and revisit sections as often as necessary. Including quality control checklists in your instructions further helps minimize errors and rework.
- Accessibility: One of the most significant limitations of paper instructions is that employees must always have bulky manuals with them on hand. When 3D guided instructions are available through mobile apps on devices they already carry, such as their smartphones or tablets, workers can review them anytime and from any place. If WiFi is unavailable, make sure to download instructions before going offline.
All these factors highlight the critical role that digital work instruction will play in optimizing business operations.
Benefits of Implementing Guided Work Instructions Software
Guided work instructions software streamlines your processes and creates an environment that’s more conducive to employee success. There are several advantages to employing this kind of technology.
Enhancing Employee Performance and Engagement
Guided work instruction software boosts productivity on multiple fronts. First, employees won’t face unnecessary delays because they search for paper-based documents or wait for supervisor responses. Granting instant access to expert knowledge and technical training allows them to focus on the task at hand, so they can do their jobs more quickly without sacrificing quality and accuracy.
When they feel supported, your employees will also feel more engaged in your organization and its success. Providing a strong, fully developed training system reflects your investment in your team and motivates them to improve their performance.
Standardization in Training
Offering all your employees the same instructional materials is vital to ensuring that they follow the right steps, processes, and procedures while completing tasks. Guided work instruction software creates uniform instructions that reduce errors, misunderstandings, and miscommunications. It also helps eliminate concerns about employees using outdated information that doesn’t reflect current practices or technologies in your organization. No matter their location or schedule, employees will have the tools they need to meet your company’s expectations.
Creating Interactive and Alternative Learning Options
Training and instructions that ignore differences in workers’ learning needs can undermine their performance and your operations. Learners struggling to understand a set of instructions might feel discouraged or disengaged from their training. This is a common problem, with 31% of organizations in a 2023 report saying that their biggest training challenge is a lack of learner engagement.
Guided work instruction software addresses these concerns because it includes various elements, such as interactive animated images, text, and audio prompts, that suit the needs of employees with different learning preferences. Rather than simply reading instructions or looking at static images, employees can engage with content in a way that plays to their strengths.
In addition, organizations can use this type of software to provide learners with different options for working through the material. For example, for a single process, they might have the option to read the instructions, listen to prompts, and interact with 3D models to examine a product or component from every angle.
Centralized Knowledge Management
Filing drawers full of instruction manuals, guidelines, and protocols makes it difficult for workers to find the information they need when they need it. Guided instruction software centralizes your training materials so employees won’t get frustrated trying to find the right documents.
This approach to knowledge management also fosters a more collaborative work environment. When employees communicate about a task or ask each other for support, they’ll be on the same page about exactly what your organization wants them to do because they’re all drawing information from one central source.
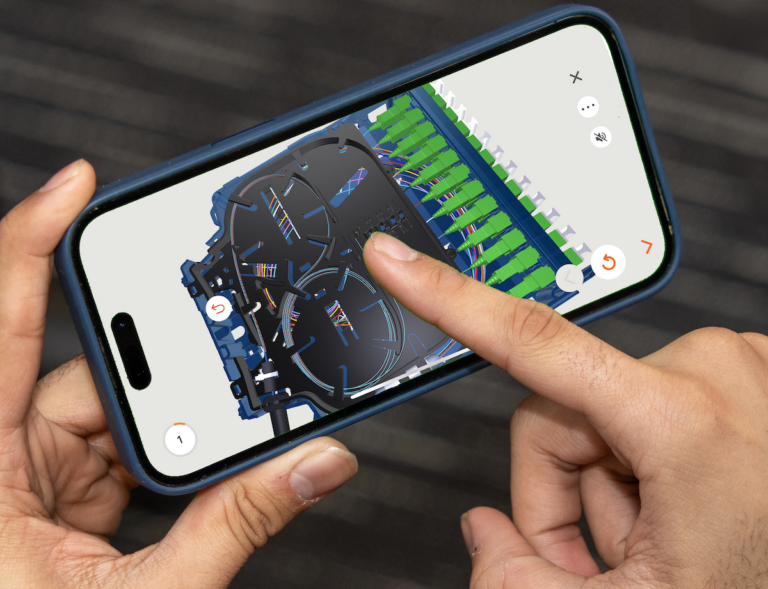
Criteria for Choosing Guided Work Instruction Software
Once you decide to make the switch to digital work instructions, the next step is to find the right solution. While many options are available on the market, it’s important to narrow them down to those offering the ideal learning structure for your team.
- Ease of use: Work instructions and the distribution platform should be intuitive for both program managers and end-users.
- A focus on safety: Your training programs should prioritize safety, competency, and efficiency. This includes developing safety measures that adhere to government, industry, and company standards, protecting your employees, and lowering the chances of compliance violations. Your work instruction software is a critical piece of your larger training program. Look for a solution that fits all your program’s various components so you can promote safe practices across the board.
- Data security: Data security should include strong measures to protect your proprietary work instructions and information.
- Integration capabilities: Select instruction software that you can seamlessly combine with your organization’s other applications and systems. This might include your enterprise resource planning (ERP) software, learning management system (LMS), or manufacturing execution system (MES). Integrating these tools simplifies the transfer of information and data, reducing the chances of inconsistencies. This results in a smooth workflow that’s straightforward for employees and more efficient for your business.
- Real-time updates: Obsolete work instructions can be worse than having no instructions at all. Find a software solution that lets you respond quickly to feedback and make real-time or near-real-time updates to your materials. Unlike updates to printed manuals or PDFs, which employees might not see for days or weeks, guided instruction software allows you to implement improvements and make them immediately available to all your employees. This helps prevent your team from working with inaccurate or outdated information and reduces the chances of time-consuming and costly errors.
- Success tracking, data, analytics, and reporting: The best-guided work instruction software solutions give you an in-depth look at the strengths and weaknesses of your current instructions and training. To do that, the software you choose should track feedback from stakeholders and trainees. It should also provide detailed reporting and analytics that are clear, relevant, and straightforward. This information is critical to your ability to evaluate and update your work instructions.
- Utilization of new technologies: When you compare instruction software, check whether a solution will allow you to create instructions that leverage the power of cutting-edge technologies. These might include 3D animations, interactive touch screens, and mixed reality. Instructions that incorporate new and emerging technologies offer a more nuanced explanation of the tasks employees or contractors need to complete. The level of engagement these technologies provide can also aid in recruiting and retaining younger or more tech-savvy workers.
Related: Buyer’s Guide to Technical Training
Extended Reality for Guided Work Instructions
The term extended reality (XR) refers to virtual, augmented, and mixed reality, which all use advanced technology to build fully or partially digital environments and interactive experiences. Using XR technologies in work instructions activates multiple senses for deeper and more lasting learning.
The Significance of Spatial Computing
Spatial computing is an important element of XR and guided work instructions. It combines virtual and augmented reality using sensors and cameras to overlay content on physical surroundings or build completely virtual environments. Spatial computing offers capabilities such as gesture-based controls, transforming how people use digital technologies to understand the world around them.
Generating Controlled Simulations With Mixed Reality
Mixed reality is a type of XR that allows users to interact with and manipulate both real-world and digital environments and objects. Organizations can use mixed reality and spatial computing to simulate complex and dangerous situations, allowing workers to safely gain hands-on experience in areas such as machine and heavy equipment operation.
Mixed reality adds another layer of interest and engagement to your instructions, and it’s particularly valuable in situations where a mistake could pose a physical or financial threat to your team or business. Some software is compatible with the Apple Vision Pro spatial computer, which offers a completely immersive experience that trains workers in a low-risk but realistic way.
XR Instructions in Action
The military is one of the most prominent organizations currently using XR training, and they’ve seen positive effects on trainees and the organization as a whole. In a 2023 survey of active duty personnel, 81% of respondents said that XR improves confidence and activates the required muscle memory for successful application. These additional statistics further underscore the advantages of using XR technology in training:
- 67% said XR makes training faster.
- 70% said it helps the military retain highly talented individuals.
- 80% said XR empowers training coordinators to be more effective.
While the military differs from a typical business, the same principles apply regarding XR and learning. Training programs and instructions that use mixed reality are often faster and more powerful than those that don’t.
Adopting a Learner-Centric Approach to Work Instruction Training
No two workers are exactly the same, and neither are their learning styles and preferences. Learner-centric instructions prioritize workers’ unique needs, intending to enhance clarity and knowledge retention.
Identifying Learning Styles
Learning occurs in several ways, and some strategies work better for certain people than others. Generally speaking, these are the kinds of learning that you should consider when designing your work instructions:
- Visual learners get the most value from videos, pictures, and graphs.
- Auditory learners learn best by listening to lectures and discussions.
- Kinesthetic learners retain more information when they participate in experiments and hands-on activities.
Remember that training is generally more effective when it combines these different types. Videos or text manuals often rely exclusively on one kind of learning, but work instruction software can pull together all three approaches.
Optimizing Understanding and Retention
Incorporating a range of teaching methods into your instructions helps meet the needs of all learners. However, according to the learning pyramid, certain approaches have higher retention rates than others:
- 5% lectures
- 10% reading
- 20% audio-visual
- 30% demonstration
- 50% discussion
- 75% practice doing
- 90% teach others
Using guided instruction software allows you to incorporate various elements impossible in standard written manuals. Most notably, software with mixed reality makes it possible to include the “practice doing” strategy.
In addition to accommodating different learning styles, it’s also important to present information in a worker’s native language. This maximizes their comprehension and helps prevent safety issues that could occur due to a language-based misunderstanding.
Related: Buyer’s Guide to Technical Training
Best Practices for Implementing Guided Work Instruction Software
Even the highest quality solution can fail if you don’t put thought into the implementation. Keep these factors in mind as you prepare to give your team access to your digital work instructions:
- Start with a pilot: Implement the software in a small area of your operations to test and refine your approach.
- Engage stakeholders early: Involve operators, technicians, and managers in the selection process to ensure the solution meets their needs.
- Focus on high-value applications: Identify processes where the software can have the most significant impact on efficiency, quality, or training.
- Target audiences and personas: Look closely at your team to determine what will work best for them, develop personas based on different workers, and strive to develop a system that will meet all their needs.
- Choose content formats: Decide what content formats you want to use, such as text, video, audio, and animation.
- Plan course schedules and locations: Determine when and where your employees will complete their training, how frequently they must participate, and whether you’ll make instructions available on demand.
- Select delivery platforms and technologies: Choose how you’ll share your work instructions with members of your organization.
- Evaluate resource requirements: Consider whether employees will need certain resources, such as computers, smartphones, or tablets, to access your instructions.
- Determine communication requirements: Make a plan for communication between you, your team, and your stakeholders, including how you’ll notify them of changes to your training materials.
- Train Your team: Invest in comprehensive training for both creators and users of the work instructions.
- Facilitate feedback and analytics: Establish a feedback loop that involves regularly evaluating and updating your training programs based on feedback, analytics, and your organization’s evolving needs.
- Iterate and improve: Use feedback and analytics to continuously refine your instructions and how they’re used.
Your guided work instruction software provider may also share additional implementation recommendations and offer one-on-one support if you encounter problems.
Examples of Guided Work Instruction Software
The use of guided work instruction software is increasingly popular in the manufacturing industry, where the order and precision of instructions can mean the difference between success and failure. Major manufacturers now use visual work instructions to train new employees and ensure existing workers follow the correct steps when repairing, installing, and building products. Some of the industries where guided work instructions can have the greatest impact include:
- Field service industries
- Heavy equipment
- Food and beverage
- Aerospace and defense
- Medical devices
Work instruction software’s applications extend beyond manufacturing. It can improve instructions and training for any organization with complicated processes. For example, visual work instructions can help professionals in trades such as construction, plumbing, and carpentry follow the appropriate and safest steps when completing a project. Similarly, military members responsible for maintaining machinery or equipment can access instructions for making a repair on the spot, even while in the field.
KPIs to Measure the Success of Your Work Instruction Software
After your work instruction software is up and running, it’s vital to regularly evaluate its effectiveness, look for weaknesses, and make updates. These key performance indicators (KPIs) will help you determine what’s working and what might need to change:
- Knowledge retention rates: Use written and practical assessments and quality control measures to determine whether workers absorb and apply the information provided in the instructions.
- Graduation or completion rates: Track the number of employees who finish their training and put their new skills into practice and the number who fail to complete the training process.
- Time to proficiency: Record the time it takes learners to complete a set of instructions or training sessions.
- Error rates and rework: Analyze mistakes that workers make on tasks where they use guided instructions. Excessive errors could indicate serious flaws in your instructional materials.
- Asset readiness: Determine whether employees can prepare assets in the way and the time frame that your organization expects.
- Team member retention: Low-quality instructions and training can drive talented employees away from your business, so keep an eye on your turnover levels and why people leave their positions.
Although your guided work instruction software isn’t the only driving force behind these KPIs, it can significantly influence them. For instance, in our Technical Training in 2024 report, 72% of executives surveyed said that high turnover is their top challenge. Team members are more likely to stay in their roles when they have quality work instructions that make them feel supported and equipped to succeed in their roles. If you discover that your work instruction software is falling short on certain KPIs, take steps to remedy those problems with the provider or start looking for a new solution that’s a better fit for your organization.
Top 10 Guided Work Instruction Software Solutions for Manufacturing and Field Service
Below are ten of the best guided work instruction software solutions, each offering unique features to enhance training and operational enablement in manufacturing:
- Dozuki provides a straightforward interface and powerful features designed for creating detailed work instructions. Its strong suit is standardization and training, making it ideal for manufacturers focused on continuous improvement and compliance.
- Tulip offers a no-code platform that allows manufacturers to create interactive, multimedia work instructions. It offers extensive integration options, making it a versatile choice for smart manufacturing environments.
- SwipeGuide delivers ease of use with its intuitive instruction design and consumption interface. The platform’s emphasis on reducing cognitive load makes complex processes simpler to execute.
- VKS (Visual Knowledge Share) offers a comprehensive solution with robust features for creating, sharing, and tracking work instructions. Its analytics capabilities are particularly strong, providing deep insights into operational efficiencies and workforce performance.
- BILT stands out for its unique approach instruction delivery with interactive 3D guidance. They create and deliver content for you. Their best-in-class instruction design practices enhance user engagement and comprehension and reduce friction and frustration. BILT is effective for complex assembly, installation, maintenance, and repair as well as its platform-agnostic field support capabilities.
- EZ Factory is known for its mobile-first approach to ensures work instructions are easily accessible to every operator. Its user-friendly design encourages continuous feedback and improvement.
- Sequence Software is tailored for ease of creating and updating detailed work instructions. It supports a wide range of media formats and offers excellent tools for revision control and compliance tracking.
- Instruqt gamifies the learning experience, making it engaging for users to follow and comprehend work instructions. This platform is ideal for organizations looking to boost engagement and retention.
- ScreenSteps is a knowledge management tool that excels in transforming complex processes into simple, actionable instructions. Its unique selling point is the rapid creation and deployment of guides.
- Whale focuses on integrating work instructions into the flow of daily work. It’s designed for fast-growing companies, offering tools for knowledge sharing, training, and ensuring standard operating procedures are followed.
Why BILT Stands Out
In a sea of digital transformation tools and platforms, BILT’s focus on 3D interactive instructions to guide work on mobile devices and 3D immersive instructions geared toward training on Apple Vision Pro set it apart from other options. Instructions can be downloaded for use without Wi-Fi. The iOS, visionOS, Android and Microsoft apps are available worldwide in 12 languages. Millions of consumers and professionals use BILT to deliver guidance for thousands of products from hundreds of brands.
The award-winning platform is a user-friendly, engaging, and effective solution for work instructions. Its ability to reduce cognitive load, personalize the user experience, and enable user feedback to manufacturers make it not just a tool but a comprehensive solution for enhancing operational efficiency and quality.
Enhance Your Operations with Digital Work Instructions
In the quest for operational excellence, digital transformation is no longer optional. Work instruction software stands at the forefront of this transformation, offering manufacturing operations a path to enhanced efficiency, accuracy, and agility. By choosing the right platform and following best practices for implementation, manufacturers can unlock significant value, driving continuous improvement and competitive advantage.
Whether you prioritize ease of use, integration capabilities, multimedia support, or analytics, there’s a solution among the top 10 that can meet your manufacturing needs. Embracing digital work instructions is not just about keeping pace with technological advancements—it’s about setting a new standard for operational excellence in your manufacturing processes.
Request a demo to see how BILT’s guided work instruction software can benefit your employees and your organization.