Fear. Anxiety. Dread. These are emotions many of us associate with product assembly and installation. After all, who hasn’t had a project go horribly wrong? Those memories leave a lasting impact. We may even avoid or delay a subsequent purchase that requires a complex setup.
The problem often lies with traditional instructions—the poorly written (or badly translated) small text, folded, paper manuals with confusing illustrations and conflicting verbiage. BILT transforms that nightmare scenario into a 3D pathway to success.
And it all begins with our design team.
High Standards for Instruction Designers
When BILT hires designers, we look beyond engineering or technical skills. We seek core traits such as intelligence, curiosity, determination, awareness, and, most importantly, empathy. Our designers hone the ability to put themselves in the position of the DIY consumer or professional trainee. In other words, BILT designers see what the customers see, think what they think, and feel what they feel.
“Every product angle, every movement I animate is to give the customer a better experience. They’re always top of mind,” says Matt Ohnesorge, BILT Senior Designer.
To do this, our designers go through every assembly, installation, maintenance, and repair step by step. They experience all the pain points from wrap rage to leftover part anxiety. They use the brand’s printed and video instructions as a baseline and discover the stumbling blocks. Then they fix them, so users don’t have to stumble behind them.
“My job is to help people be less frustrated. If there’s anything this world needs it’s less frustration,” says Patrick Falenofoa, BILT Lead Designer.
“I think there’s a misconception that BILT designers must be amazing at following 2D directions, but that’s not the case. We make mistakes, too, as we go through the process,” says Stephanie Raptis, BILT Lead Designer. “If BILT wanted engineers, they would have hired engineers. But engineers wrote the 2D instructions, and that’s where a lot of the problems come into play.”
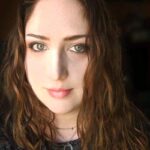
Proactively Finding and Solving Problems
Our designers are resilient puzzle solvers. They’re adept at anticipating—and fixing—potential problems created by product design or instruction flaws. It’s a process known as continuous improvement. BILT designers make the instructions better so your customers or teams don’t have to deal with the same headaches.
For example, when assembling an end table, the BILT designer may determine the steps should be reordered to make the project flow better, or that the weight of a component might lend it to being put together first. Maybe there are similar looking screws that are slightly different sizes that could be easily confused and need to be called out. Sometimes tools should be used in a specific way or pressure must be applied in order for the holes to line up appropriately. Designers must address whatever complexities they encounter along the way to prevent users from experiencing the same difficulties.
“Our designers must become experts in assembling or installing a product they’ve never worked on before while maintaining the understanding of what it felt like to experience the process for the first time,” says Mike Wencel, BILT Senior Vice President of Instruction Design. “And then they must pass that learning experience to our users.”
Performing Assembly Analysis
As part of their assembly analysis, our designers take detailed notes throughout their journey. They make recommendations to manufacturers, perhaps adding or consolidating steps to make the instructions clearer. They may add arrows, animate movement, or include other directional prompts. They may flip an object around for an optimal view. When working with prototypes, our designers have identified design flaws and alerted the manufacturer, saving the brand time and money in reengineering the product before it becomes a much bigger problem.
“We come to understand the products so well the brands trust us,” says Sarah Rich, BILT Lead Designer.
The goal is to identify and overcome these pain points, so your users are treated to a smooth, stress-free experience. When our designers reach the final step, sometimes they’re more familiar with the product than the manufacturer. It’s that thorough a process.
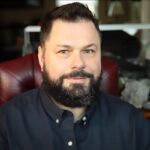
Designers: Our “BILT-In” Advantage
By painstakingly going through every installation and assembly process just like your customers would, our designers ensure BILT’s guides are superior to paper manuals and video instructions. We’re not just digitizing the original instructions in 3D form. We improve them to make the process simpler, faster, and more fun. We also highlight any steps that could become potential safety issues.
BILT may be built on technology. But it’s powered by people—bright, thoughtful, inquisitive, meticulous, empathetic individuals—dedicated to positively impacting the lives of your customers.
To learn how your products can be a part of this impactful experience, please contact our sales team.