Training employees in industrial settings presents unique challenges, including dealing with complex machinery, toxic substances, and hazardous conditions. However, an effective training program is essential to prevent potentially dangerous and costly accidents and errors.
Extended reality (XR) and immersive instructions offer a revolutionary way to strengthen training systems for field services and sidestep these obstacles. This article explores how integrating XR training into work instruction software can benefit both your organization and workers.
Understanding Extended Reality (XR) Training For Industrial Workers
The term XR encompasses several different technologies:
- Virtual reality (VR) is completely simulated. Your employees can immerse themselves in an environment that mimics their physical workspace.
- Augmented reality (AR) combines virtual elements with physical environments. Employees can see digital objects, data, videos, and graphics overlaid on their actual surroundings.
- Mixed reality (MR) is similar to AR in that it combines virtual objects with the real world. However, employees using mixed reality can interact with both physical and digital elements, and these elements can also interact with one another.
- Spatial computing was introduced as a concept with the release of Apple Vision Pro. Spatial computing technology allows humans to interact with computers in a three-dimensional space, such as using an Apple Vision Pro to manipulate virtual 3D models in real work environments.
Many industrial organizations are leveraging one or more types of XR technologies to enhance their work instructions and provide more effective training for their teams. By incorporating XR, these organizations can offer immersive, interactive, and highly engaging training experiences.
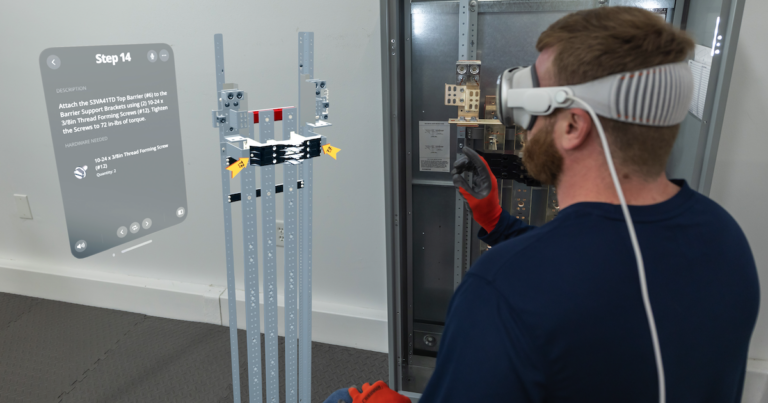
XR Training Benefits for Your Work Instruction Software
XR training has many advantages over more traditional training methods. The benefits extend not only to your trainees but also to your business as a whole.
Inclusivity
Many training methods, such as paper manuals, videos, and demonstrations, only meet the needs of a few learners. Manufacturing training with XR technology creates a positive, supportive training experience for everyone because it incorporates multiple learning styles, including:
- Visual: Incorporates graphics, models, and written instructions
- Auditory: Uses virtual and real-life sounds, along with spoken instructions
- Kinesthetic: Enables employees to touch and interact with both digital and physical objects
Combining multiple learning styles into your digital work instructions means that your employees can interpret the material in a way that suits their individual strengths and preferences. Because it accommodates the widest range of learners, XR technology also helps trainers provide the best possible learning experience and improve employee ramp time.
In a 2023 study by the U.S. military, 80% of respondents said that XR empowered trainers to be more effective. XR not only enhances the learning experience for employees but also significantly boosts the trainers’ ability to teach complex concepts and procedures efficiently.
Improved Outcomes
Digital work instruction software that leverages XR is more engaging because it’s interactive, unlike reading about or watching a task. Trainees are actively involved in the learning process, so they can form lasting memories and have much higher knowledge retention.
Trainees can also practice tasks as many times as they want because they aren’t using physical resources. This repetition contributes to a deeper understanding and greater confidence in their abilities. These same results played out in the military, with 81% of respondents saying that XR increased their confidence and cultivated muscle memory.
Safe and Realistic Simulations
XR training dramatically improves the safety of industrial training without decreasing the quality of the learning experience. In the military study, 67% of respondents said XR training helps them better prepare for stressful situations. That’s because it simulates real-world experiences, so employees know what to expect from their work in the future.
At the same time, because the objects they use during training are partially or fully virtual, there’s a much lower risk that trainees will cause any damage to property. With immersive technology, they’ll be less likely to suffer or cause injuries when learning how to handle dangerous tools or equipment.
Simplified Hands-On Learning
In the past, the typical industrial training experience required employees to repeatedly refer to their manuals to find out what they should do next. XR training eliminates this need by overlaying step-by-step instructions and vital information over the trainee’s environment. Your employees can focus on their tasks without having to look away, search for the next step, or interpret printed diagrams or graphics.
Recruitment
The opportunity to learn with XR is very appealing to potential job candidates. Many modern workers are looking for advanced training programs that go beyond printed manuals and tests on a computer. The military has seen the power of XR play out in their own recruiting, with 74% saying XR training provided a recruitment edge and 70% reporting it helped them retain top talent.
Cost-Effectiveness and Efficiency
Finally, XR training programs can save businesses considerable time and money. While many other types of training programs involve a lot of wasted or damaged resources, trainees using XR only need access to their devices. Digital work instruction software with XR also accelerates the pace of training.
In the military survey, 76% of respondents said that XR allowed trainees to complete their training faster. XR technologies can offer significant efficiency gains across various industries, demonstrating its potential for widespread adoption and impact on training methodologies.
Integrating XR Training into Your Work Instruction Software
For many companies, implementing XR into your training for industrial workers or work instruction software can seem overwhelming. To get started, focus on these key factors:
- Selecting the right XR training solution for your specific industrial needs
- Creating an integration plan that outlines your timeline, budget, and resources
- Giving employees time to adopt and adapt to this innovative training approach
The switch to XR doesn’t happen overnight. It will take time for your organization and your team to adjust, but remember that it will ultimately streamline and upgrade your training program.
Bridge the Skills Gap With the Help of BILT
With a focus on user-friendly, engaging, and effective work instructions, BILT offers the best XR solutions for manufacturing training. Your trainees can access interactive 3D work instructions on mobile devices or experience 3D immersive instructions on Apple Vision Pro.
BILT also allows your employees to download instructions, so they can participate in training no matter where they’re located. Request a demo to learn more about how BILT can reduce your employees’ cognitive load, personalize their user experience, and support their success.