Effective work instructions are critical for building a successful team that consistently produces high-quality work. Unfortunately, many companies that rely on outdated instruction and training methods put their employees and their operations at an enormous disadvantage, potentially resulting in costly errors, wasted time and resources, and quality concerns.
Upgrading your work instructions to a digital format is an easy way to remedy these issues. With digital work instructions software, you can offer employees access to modernized instructional materials that allow for a level of interaction and engagement that isn’t possible with printed instructions.
Moving away from traditional manuals to paperless work instructions enhances your operations, makes your training more effective, and keeps your employees safer. Here are six key signs that show you’re ready for digital work instructions.
1. Outdated or Inefficient Processes
The first sign that it’s time to change your work instruction strategy is if your current methods are creating more problems than they solve. For instance, printed manuals are often difficult and time-consuming to update. You not only have to make corrections and additions to the documents but also develop a replacement plan that ensures everyone receives the revised version.
Relying solely on verbal instructions without any visual aids in the field also creates challenges. Research shows that visuals can improve learning by up to 400%, so training employees without providing visual reinforcement could lower their comprehension and knowledge retention levels.
Ultimately, using outdated and inefficient work instruction processes can negatively affect your operations, causing excessive manufacturing errors, rework, and delays. Digital work instructions can address these issues by providing mobile 3D visuals and interactive instructions, enhancing employee training, and improving overall efficiency.
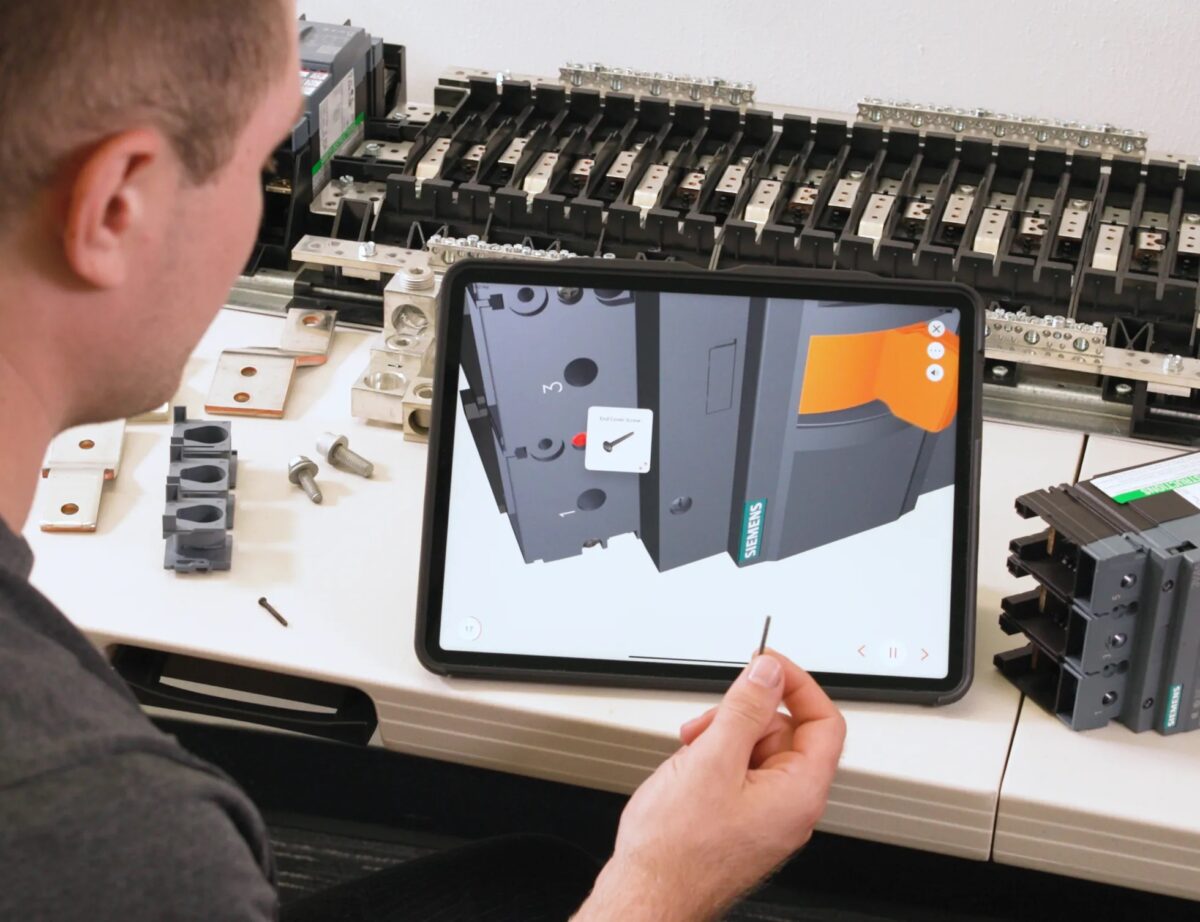
2. Lack of Standardization
To maintain a high level of quality across your operations, your employees should all receive the same information about what steps they should follow and how to meet your company’s standards. Inconsistent instructions can confuse your team and result in varied outcomes when performing tasks in the field.
This is a common problem if you use printed instructions because employees may have different versions of them. For example, an employee who has been with the company for a decade might rely on an old manual rather than looking at the newest version, whereas a new employee won’t have any knowledge of past procedures or requirements. Even small differences can cause misunderstandings and make it harder to collaborate.
With digital work instructions, every employee will have access to the same information. Standardization ensures product quality and compliance with internal and external standards and regulations. It also fosters trust and cooperation between your employees as they’ll have a shared understanding of the practices within your organization.
3. Difficulty in Updating Instructions
Keeping paper instructions up-to-date is logistically challenging, especially when it comes to distribution. In addition to passing out your updated manuals, you also have to announce the changes and confirm that employees have turned in or destroyed any past versions in their possession. Printing and giving out new instructions can also get expensive if you make frequent changes. As a result, some companies neglect to regularly add new information or improved instructions to their manuals, which contributes to work errors and inefficiencies.
Digital work instruction software enables fast and easy near real-time updates. Technicians will always have the latest information, and you won’t waste time or money producing and handing out manuals. In addition, you can make changes as often as you want, ensuring you provide the best possible instructions to employees at all times.
4. Limited Accessibility
One of the most frustrating aspects of paper-based instructions is that they’re not always close by when you need them. For instance, an employee who uses a hard-copy manual might not have access to it while in the field, which is precisely the time when they may need it most.
Making instructions readily available to field technicians—even those working in remote locations—allows them to complete their work more quickly and accurately. With digital 3D work instructions, these employees can use mobile devices to access the information they need regardless of where they’re working.
5. Poor User Engagement in Training
If you find that your employees regularly fail to follow the steps outlined in their paper manuals or struggle to pay attention to training sessions, a digital transformation could be the solution. Interactive work instructions are more engaging, regardless of whether employees are using them during training, on the floor, or in the field.
Digital instructions are distinct from paper-based manuals because they cater to multiple learning styles, including auditory, visual, and kinesthetic learners, with active participation and multimedia content. As a result, your employees are more likely to pay close attention, fully understand the material, stick to your established processes, and increase productivity.
6. High Safety Risks and Errors
Work instruction software for manufacturing and other industries also serves the essential goal of protecting employees from dangerous errors that could put their health or well-being at risk. Unclear or outdated instructions can lead to mistakes and create hazardous conditions. They also increase the chances that your employees will violate safety regulations, which could result in fines or penalties for your company.
Work instruction software reduces these risks by providing clear, updated guidance. With real-world simulations, employees can learn from their mistakes in a low-risk environment. Improved instructions help safeguard your team and keep your organization in compliance.
Digitize Your Work Instructions With BILT
If you’re ready to bring your work instructions into the modern era, BILT is ready to help. With user-friendly, engaging, and effective work instructions, BILT’s digital work instruction software reduces your employees’ cognitive load and personalizes their experience. The option to download instructions for use without Wi-Fi means that your employees and field technicians can access instructions on the go.
BILT also accommodates the needs of different industries and learning styles by offering 3D interactive instructions to guide work on mobile devices and 3D immersive instructions geared toward training on Apple Vision Pro.
Request a demo to see how interactive work instructions can maximize your employee training and business performance.