The field services industry is going through significant upheaval, and companies are looking for ways to weather the storm of the silver tsunami. As the workforce ages, younger generations are replacing older, more experienced technicians. This creates a troubling gap in skill levels that can affect employee performance and work quality.
One of the keys to bridging the skills gap is technology, particularly 3D work instructions. Using digital work instruction software, field technicians gain the skills and knowledge they need to excel in their roles, regardless of whether they’re new or have been in the industry for decades. This article will walk you through five of the biggest obstacles in field service management and explain how 3D work instructions can help overcome them.
1. Complex Equipment Repairs
Field service technicians often have to perform repairs on intricate machinery and systems. To ensure they can tackle these kinds of tasks, they need extensive technical knowledge and excellent recall of information. This is especially problematic for workers who recently entered the field, as they don’t have years of practice to draw and learn from.
3D work instructions provide clear, step-by-step visuals that guide a field worker through complex repair processes. Rather than relying on memory alone, they can refer to digital work instructions any time they have questions or are unsure what to do next, allowing them to get repairs done quickly and correctly the first time. This not only enhances the efficiency of the repair process but also boosts the confidence and capability of less experienced technicians.
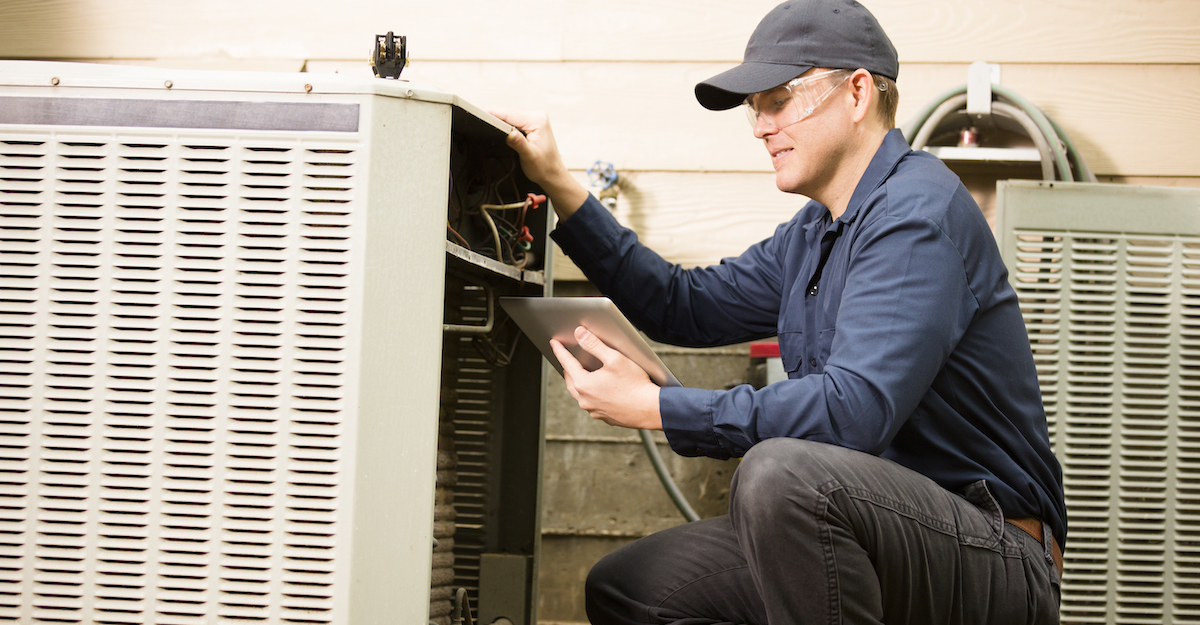
2. High Training Costs and Time
The field services industry faces growing concerns about labor shortages, increasing each year as a significant portion of the workforce nears retirement age. Nearly half of field technicians in North America are over 50 years old, meaning retirements in the coming years could significantly outpace new hires. To keep up, companies need to train new technicians rapidly and effectively. However, the fast-paced environment and the high cost of raw training materials pose logistical and financial problems.
Work instruction software enhances training, making it faster and more effective. 3D work instructions serve as interactive learning tools with visual aids that reduce the need for lengthy and costly training sessions while providing better outcomes and knowledge retention. Additionally, immersive technology allows trainees to practice and develop their skills using digital objects, avoiding the risk of damaging physical equipment during the training process. Not only does this save time and money but also prepares technicians more thoroughly for real-world scenarios.
3. Difficulty in Accessing Information On-Site
In the past, technicians often turned to paper manuals to guide them through repair steps, but that approach is inconvenient and inefficient at best. Technicians who forget, lose, or damage their manuals will find themselves without the resources they need when they arrive at job sites. They might also struggle to read paper instructions while trying to perform a repair, and if the instructions aren’t clear, they have to waste valuable time talking to customer support.
Unlike traditional manuals, mobile-enabled 3D work instructions are available on the go. Technicians can easily access the information they need from their devices—even in the most remote locations. With the right guidance always at their fingertips, they can perform their jobs more efficiently and consistently. This eliminates the dependency on physical manuals and ensures that technicians are well-equipped to handle any situation they encounter on-site.
4. Communication Barriers
Technicians sometimes struggle to communicate with other people in field service operations. Different languages, scheduling conflicts, workloads, and preferences can make it more difficult for technicians to understand their instructions or get assistance from their coworkers. Unfortunately, misinterpreting written and spoken instructions can lead to significant problems, including potentially dangerous or costly mistakes on the job.
Because they include visuals, 3D work instructions transcend language barriers. BILT’s digital work instruction software also supports multiple languages, enabling a diverse workforce to fully understand and follow procedures. As a result, all technicians can access clear and accurate instructions, reducing the risk of errors and enhancing overall job performance.
5. Safety and Compliance Issues
Safety and compliance are top priorities in field operations. Companies have to adhere to regulations to avoid penalties and potential downtime. More importantly, workers who follow safety standards are less likely to suffer injuries on the job.
Despite their best efforts, many technicians fail to adhere to safety protocols and regulatory requirements because they don’t fully understand them or are unaware of recent changes. Paper manuals are notoriously time-consuming and frustrating to update, not to mention confirming that every technician receives and uses the latest version of their instructions.
Interactive work instructions improve field service work in terms of safety and compliance in multiple ways. First, they can incorporate safety reminders and compliance checks within the instructions. These additional features help keep safety and compliance at the forefront of the technicians’ minds while they work. This decreases the chances that they’ll encounter issues that result in unnecessary hazards or compliance violations.
In addition, digital work instruction software enables real-time updates to instructions. Rather than editing, printing, and handing out new manuals whenever a change occurs, field service management can instantly revise instructions to reflect the latest standards and regulations.
Elevate Field Technician Performance With BILT
A 2024 study by Aquant found that low-performing field services employees can cost up to 80% more than top-performing workers. With so many experienced technicians permanently leaving the workforce, it has never been more important for companies to provide effective training and instructions. Leveraging new technologies is one of the most effective ways to achieve that goal, allowing you to provide shorter training and more effective field support.
BILT is designed for professionals and offers digital, 3D work instructions that field technicians can use for initial training, job site review, and troubleshooting. Technicians can access BILT’s instructions in 12 languages on their mobile devices and download them for use when Wi-Fi is unavailable.
On top of those benefits, BILT’s work instruction software also reduces cognitive load, adapts to different learning styles, and enables user feedback to manufacturers. Request a demo to see how BILT can help improve your employees’ training and efficiency.